Princeton Scientists Create Innovative New Material: Stretchable, Flexible, And Recyclable
Nanoscale Structure and Material Properties
The material's exceptional performance is rooted in its internal structure at the nanoscale. The research team utilized a block copolymer that forms rigid cylindrical structures, each measuring 5-7 nanometers in diameter (for context, human hair is approximately 90,000 nanometers thick), embedded within a flexible polymer matrix. Through 3D printing, these nanoscale cylinders were precisely aligned, resulting in a material that is rigid in one direction while being soft and stretchable in nearly all others. By adjusting the orientation of these cylinders within a single object, designers can create materials with varying stiffness and stretchiness across different regions.
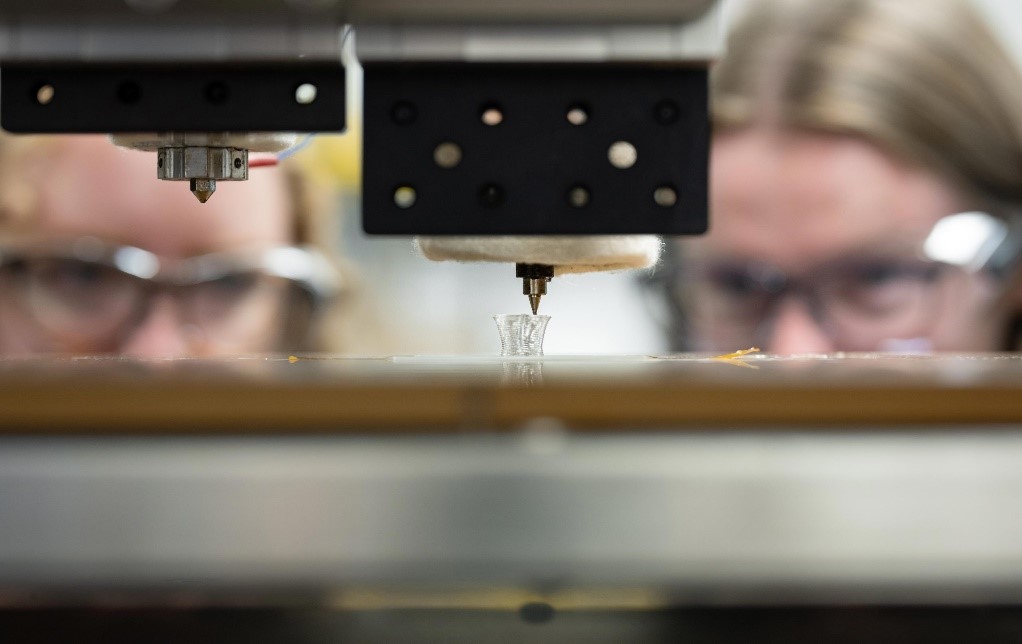
Figure 1. Princeton Scientists Develop Groundbreaking Stretchable, Flexible, and Recyclable Material
"The elastomer we are using forms nanostructures that we can control," explained Davidson. This capability provides designers with significant flexibility in crafting materials with tailored properties in various directions. Figure 1 shows Princeton Scientists Develop Groundbreaking Stretchable, Flexible, and Recyclable Material.
Choosing the Right Polymer
The first step in developing this process involved selecting the ideal polymer. The researchers opted for a thermoplastic elastomer, a block copolymer that can be melted and processed when heated, then solidifies into an elastic material upon cooling. At the molecular level, polymers consist of long chains of linked molecules. Traditional homopolymers are made of one repeating molecule, while block copolymers contain different homopolymers connected together. These distinct regions in a block copolymer behave like oil and water, separating rather than mixing. The researchers leveraged this property to create a material with stiff cylinders embedded in a flexible matrix.
3D Printing Technique and Thermal Annealing
Building on their understanding of how block copolymer nanostructures form and respond to flow, the researchers developed a 3D printing technique that aligns these rigid nanostructures effectively. They studied how printing speed and controlled under-extrusion could influence the physical properties of the printed material.
Thermal Annealing and Self-Healing Properties
“I think one of the coolest aspects of this technique is how thermal annealing plays multiple roles — not only does it significantly enhance the material's properties after printing, but it also makes the printed items reusable multiple times and capable of self-healing if damaged or broken,” said Fergerson.
Affordability and Functional Additives
Davidson explained that one of the project's main objectives was to create soft materials with locally tunable mechanical properties in a way that is both cost-effective and scalable for industrial use. While materials like liquid crystal elastomers can achieve similar effects with locally controlled properties, they are costly (around $2.50 per gram) and require complex, multi-step processes involving controlled extrusion and ultraviolet light exposure. In contrast, the thermoplastic elastomers used in this research cost about a cent per gram and can be printed using a commercial 3D printer.
The researchers also demonstrated the ability to incorporate functional additives into the thermoplastic elastomers without compromising the control over material properties. For instance, they added an organic molecule from Professor Lynn Loo’s group that causes the plastic to glow red after exposure to ultraviolet light. Additionally, they successfully printed complex, multi-layered structures, including a tiny plastic vase and printed text that cleverly spelled out "PRINCETON" with sharp turns.
A Major Milestone in Automotive Manufacturing
Building on their success with multi-material bonding, the research team has now prototyped the world's first full-scale automotive multi-material component: a suspension tower. This innovative part features a tailored geometry, offering both reduced weight and increased strength. The breakthrough has wide implications for the future of automotive manufacturing, as the team plans to apply these findings to other metal combinations facing similar bonding challenges. This could lead to broader adoption of lightweight, high-strength components in vehicles, driving the future of more efficient and sustainable automotive designs.
Self-Healing and Future Applications
Annealing plays a crucial role in perfecting the internal nanostructure arrangement. According to Davidson, annealing also enables the self-healing properties of the material. The researchers showed that by cutting a flexible sample and then reattaching it through annealing, the material restored its original properties. They observed “no significant differences” between the original and the repaired sample.
Looking ahead, the team plans to explore new 3D printable architectures that could be applied to wearable electronics and biomedical devices.
Source:SciTECHDaily
Cite this article:
Priyadharshini S (2024), Princeton Scientists Create Innovative New Material: Stretchable, Flexible, And Recyclable, AnaTechMaz, pp. 89