Japanese Scientists Reveal Revolutionary 3D Printing Breakthrough for Lightweight Cars
Metal 3D printing involves constructing objects layer by layer, bonding metal layers using heat. This method offers exceptional precision, enabling the creation of unique, highly customizable shapes while reducing material waste compared to traditional manufacturing processes.
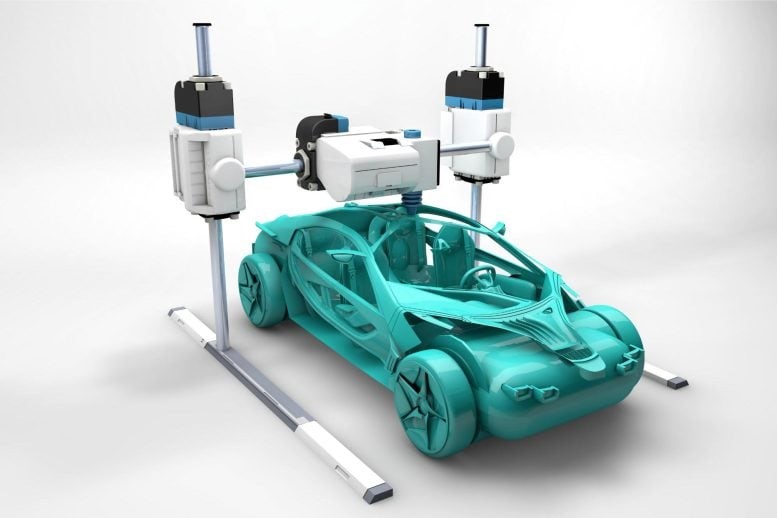
Figure 1. Revolutionary 3D Printing Breakthrough for Lightweight Cars Unveiled by Japanese Scientists.
Steel-Aluminium Alloy Interfaces
A key benefit of 3D printing is the ability to create "multi-material structures," which combine different materials to optimize component performance. For example, incorporating aluminum with steel in automotive parts can greatly reduce weight without compromising strength. These advantages have made advanced 3D printing techniques a focal point for researchers globally, offering vast potential for innovation in manufacturing. Figure 1 shows Revolutionary 3D Printing Breakthrough for Lightweight Cars Unveiled by Japanese Scientists.
However, challenges remain. "Multi-materials are a hot topic in additive manufacturing due to its process flexibility," explains Associate Professor Kenta Yamanaka (Tohoku University). "Yet, a major challenge is that certain metal combinations, such as steel and aluminum, can form brittle intermetallic compounds at the dissimilar metal interfaces. This can result in a lighter material, but it becomes more brittle."
Overcoming Challenges: Laser Powder Bed Fusion (L-PBF)
The aim of this study was to develop a lightweight steel-aluminum alloy without sacrificing strength. To achieve this, the research team utilized Laser Powder Bed Fusion (L-PBF), a leading metal 3D printing technology that uses a laser to selectively melt metal powders.
Through their experiments, they found that increasing the laser scan speed significantly reduced the formation of brittle intermetallic compounds (such as Al5Fe2 and Al13Fe4). They proposed that the faster scanning speed causes non-equilibrium solidification, which minimizes solute partitioning and prevents the creation of weak points in the material. As a result, the product demonstrated strong bonding interfaces, improving both the material's strength and durability.
"In other words, you can’t just slap two metals together and expect them to stick without a plan," says Specially Appointed Assistant Professor Seungkyun Yim (Tohoku University). "We had to fully understand the in-situ alloying mechanism first."
Building on this success, the team successfully prototyped the world’s first full-scale automotive multi-material component (a suspension tower) with a custom-designed geometry. The research group plans to apply these insights to other metal combinations that face similar bonding challenges, paving the way for broader applications in manufacturing.
A Major Milestone in Automotive Manufacturing
Building on their success with multi-material bonding, the research team has now prototyped the world's first full-scale automotive multi-material component: a suspension tower. This innovative part features a tailored geometry, offering both reduced weight and increased strength. The breakthrough has wide implications for the future of automotive manufacturing, as the team plans to apply these findings to other metal combinations facing similar bonding challenges. This could lead to broader adoption of lightweight, high-strength components in vehicles, driving the future of more efficient and sustainable automotive designs.
The Promise of Metal 3D Printing for Automotive Innovation
Japanese scientists have achieved a groundbreaking advancement in 3D printing technology, focusing on creating lightweight automotive parts. Metal 3D printing, particularly techniques like Laser Powder Bed Fusion (L-PBF), allows for the construction of highly precise and customizable components by building them layer by layer. This method helps reduce material waste compared to traditional manufacturing processes. By using advanced 3D printing, engineers can combine materials like steel and aluminum, achieving a perfect balance between weight reduction and strength—key factors in automotive design.
Source:SciTECHDaily
Cite this article:
Priyadharshini S (2024), Japanese Scientists Reveal Revolutionary 3D Printing Breakthrough for Lightweight Cars, AnaTechMaz, pp. 88