How to Overcome Bottlenecks in CO2 Capture and Conversion
Efficiently removing carbon dioxide from the atmosphere is widely recognized as a critical strategy for addressing climate change. However, current CO₂ removal systems face a fundamental tradeoff: chemical compounds that capture CO₂ effectively tend to hold onto it tightly, making release difficult, while those that release CO₂ easily often do so at the expense of capture efficiency. Enhancing one stage of the process typically compromises the other.
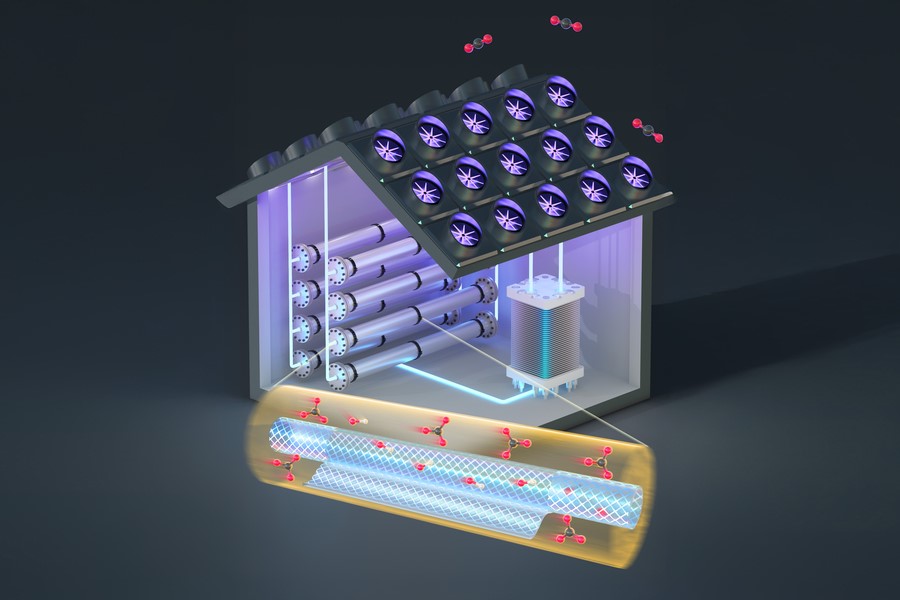
Figure 1. Overcoming Key Challenges in CO₂ Capture and Conversion.
Researchers at MIT have now introduced a novel solution using nanoscale filtering membranes, adding a simple intermediate step that improves both capture and release. This innovative approach could boost the efficiency of electrochemical CO₂ capture and release by up to six times, while reducing costs by at least 20 percent. Figure 1 shows Overcoming Key Challenges in CO₂ Capture and Conversion.
“We need to consider scale from the very beginning when it comes to carbon capture, since making a meaningful impact requires processing gigatons of CO₂,” says Varanasi. “This perspective helps us identify critical bottlenecks and develop innovative solutions with real-world impact. That’s what drives our work.”
Many carbon-capture systems rely on hydroxide chemicals that readily bind with carbon dioxide to form carbonate. This carbonate is then fed into an electrochemical cell, where it reacts with an acid to produce water and release pure CO₂. This process can extract CO₂ from ambient air—where it exists at just about 400 parts per million—and produce a stream of nearly 100% pure carbon dioxide, useful for fuels and other products.
Both capture and release steps occur in the same water-based solution, but they require different chemical environments: the capture step needs a solution rich in hydroxide ions, while the release step needs one rich in carbonate ions. “These two steps work against each other,” explains Varanasi. “They cycle the same sorbent liquid back and forth, but because each step needs a different optimal solution, neither can operate efficiently at the same time.”
To solve this, the team introduced a third stage between the two. After most hydroxide ions convert to carbonate, special nanofiltration membranes separate ions by their charge—carbonate ions carry a charge of 2, while hydroxide ions carry a charge of 1. “The nanofiltration does a good job separating these ions,” says Rufer.
Once separated, the hydroxide ions are recycled back to the absorption side of the system, while the carbonate ions move forward to the electrochemical release stage. This separation allows both parts of the system to operate in their optimal conditions. Varanasi explains that during the electrochemical release, protons are added to carbonate ions to generate carbon dioxide and water. However, if hydroxide ions are present, the protons react with them instead, producing only water and reducing CO₂ extraction efficiency.
“If you don’t separate hydroxides from carbonates,” says Rufer, “the system fails because protons target hydroxides rather than carbonates, wasting energy by making water instead of releasing CO₂. Using nanofiltration to prevent this is a novel approach, as far as we know.”
Testing demonstrated that the nanofiltration membrane could separate carbonate from hydroxide ions with about 95% efficiency under realistic conditions. The team then developed a techno-economic model incorporating factors like electrochemical efficiency, voltage, absorption rate, capital costs, and nanofiltration performance.
Their analysis showed that current systems cost at least $600 per ton of CO₂ captured, but with nanofiltration, that drops to around $450 per ton. Moreover, the new system is much more stable and tolerant to fluctuations in ion concentrations. “Without nanofiltration, you’re operating on a knife’s edge,” Rufer notes—small changes drastically reduce efficiency. “With nanofiltration, the system acts as a buffer, broadening the operational range and lowering costs.”
This method could be applied beyond direct air capture to point-source capture—such as power plant emissions—and to subsequent stages like converting CO₂ into fuels or chemicals, which also face the carbonate-hydroxide tradeoff.
Varanasi adds that the technology may enable safer carbon-capture chemistries. “Some absorbents are toxic or environmentally harmful. Our system improves reaction rates, allowing the use of safer chemicals that initially absorb less efficiently but perform better overall.”
Importantly, the team used commercially available membranes, enabling easy retrofitting of existing carbon-capture setups. If costs can be reduced to around $200 per ton, widespread adoption becomes feasible. “With ongoing work, we’re confident this approach can become economically viable,” says Varanasi, “ultimately producing valuable, marketable products.”
Rufer points out that carbon credits currently sell for over $500 per ton. “At our projected cost, the system is already commercially viable for some buyers. Lowering the price further will expand the market.” Varanasi concludes, “Our goal is to deliver scalable, cost-effective, and reliable technologies that help industries meet their decarbonization targets directly.”
Source:MIT NEWS
Cite this article:
Priyadharshini S (2025), How to Overcome Bottlenecks in CO2 Capture and Conversion, AnaTechMaz, pp. 215