Types of 3D printing
The term 3D printing encompasses several manufacturing technologies that build parts layer-by-layer. Each varies in the way they form plastic and metal parts and can differ in material selection, surface finish, durability, [1] and manufacturing speed and cost. There are several types of 3D printing, which include:
- Stereolithography (SLA)
- Selective Laser Sintering (SLS)
- Fused Deposition Modeling (FDM)
- Digital Light Process (DLP)
- Multi Jet Fusion (MJF)
- PolyJet
- Direct Metal Laser Sintering (DMLS)
- Electron Beam Melting (EBM)
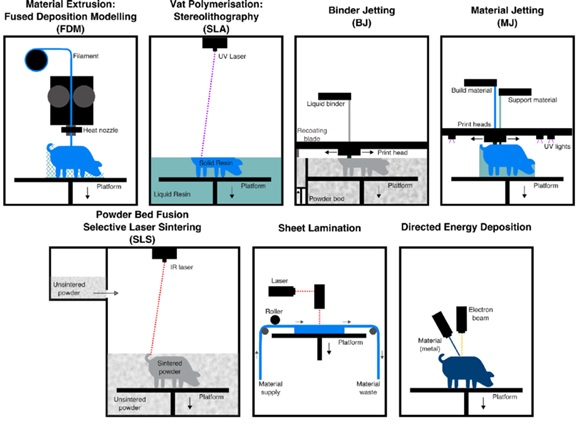
Figure 1: 3D Printing
Stereolithography (SLA)
SLA holds the historical distinction of being the world’s first 3D printing technology. Stereolithography was invented by Chuck Hull in 1986, who filed a patent on the technology and founded the company 3D Systems to commercialize it.
Fused Deposition Modeling (FDM)
Fused Deposition Modeling (FDM) is sometimes called as Fused Filament Fabrication (FFF) An FDM printer works by expelling a plastic fiber layer-by-layer onto the forming stage. It’s a savvy and fast strategy for delivering actual models. There are a few occasions when FDM can be utilized for practical testing however the innovation is restricted because of parts having generally harsh surface completes and lacking strength. It is a 3D printing innovation that utilizes a cycle called Material Extrusion. Material Extrusion gadgets are accessible and reasonable of all. They work by a cycle where a spool of a fiber of strong thermoplastic material (PLA, ABS, PET) is stacked into the 3D printer. It is then pushed by an engine through a warmed spout, where it liquefies.
The printer’s expulsion head at that point moves along explicit directions, keeping the 3D printing material on a form stage where the printer fiber cools and cements, shaping a strong item. When the layer is finished, the printer sets out another layer, until the item is complete. Basic applications for FDM incorporate electrical lodgings, structure and fit testings, jigs and fixtures, and investment casting patterns. The best part about FDM is that it offers the best surface completion in addition to full tone alongside the reality there are different materials accessible for its utilization.
Multi Jet Fusion (MJF)
Multi Jet Fusion assembles utilitarian parts from nylon powder. As opposed to utilizing a laser to sinter the powder, MJF utilizes an inkjet cluster to apply melding specialists to the bed of nylon powder. At that point, a warming component disregards the bed to combine each layer. This outcome in more predictable mechanical properties contrasted with SLS just as improved surface completion. [4] Another advantage of the MJF cycle is the quickened fabricate time, which prompts lower creation costs. MJ differs from other types of 3D printing technologies that deposit, sinter, or cure build material with point-wise deposition.
Instead, the print head jets hundreds of droplets of photopolymer and cures/solidifies them using UV light. Once a layer is deposited and cured, the build platform lowers by one layer thickness, and the process is repeated until the 3D object is built. Another difference from 3D printing technologies is instead of using a single point to follow a path that outlines the cross-sectional layer, MJ machines deposit build material in a fast, line-wise manner. Articles made with MJ need help during printing and are printed all the while during the form cycle with a dissolvable material that is taken out in post-handling. MJ is one of the solitary sorts of 3D printing innovation that can make objects produced using numerous materials and with full tone. The advantage to this is MJ printers can fabricate multiple objects in a single line without affecting build speed. As long as the models are arranged correctly with optimal spacing, MJ can produce parts faster than other types of 3D printers. Hence, there are multiple processes for multiple projects, selecting the best suitable process is of utmost importance.
Direct Metal Laser Sintering (DMLS) / Selective Laser Melting (SLM)
Both Direct Metal Laser Sintering (DMLS) and Selective Laser Melting (SLM) produce objects in a similar fashion to SLS. The main difference is that these types of 3D printing technology are applied to the production of metal parts.
DMLS does not melt the powder but instead heats it to a point so that it can fuse on a molecular level. SLM uses the laser to achieve a full melt of the metal powder forming a homogeneous part. [5] This results in a part that has a single melting temperature (something not produced with an alloy).
This is the main difference between DMLS and SLM; the former produces parts from metal alloys, while the latter form single element materials, such as titanium. Unlike SLS, the DMLS and SLM processes require structural support, to limit the possibility of any distortion that may occur (despite the fact that the surrounding powder provides physical support).
DMLS/SLM parts are at risk of warping due to the residual stresses produced during printing, because of the high temperatures. Parts are also typically heat-treated after printing, while still attached to the build plate, to relieve any stresses in the parts after printing.
Electron Beam Melting (EBM)
Distinct from other Powder Bed Fusion techniques, Electron Beam Melting (EBM) uses a high energy beam, or electrons, to induce fusion between the particles of metal powder. A focused electron beam scans across a thin layer of powder, causing localized melting and solidification over a specific cross-sectional area. These areas are built up to create a solid object. Compared to SLM and DMLS types of 3D printing technology, EBM generally has a superior build speed because of its higher energy density. However, things like minimum feature size, powder particle size, layer thickness, and surface finish are typically larger.
Also important to note is that EBM parts are fabricated in a vacuum, and the process can only be used with conductive materials.
References:
- https://www.twi-global.com/technical-knowledge/faqs/what-is-3d-printing
- https://all3dp.com/1/types-of-3d-printers-3d-printing-technology/
- https://www.futurelearn.com/info/courses/getting-started-with-digital-manufacturing/0/steps/184102
- https://formlabs.com/asia/3d-printers/
- https://www.makerbot.com/stories/design/types-of-3d-printing-technologies/
Cite this article:
Vinotha D (2021), Types of 3D printing, AnaTechMaz pp. 10