Hierarchical Micro/Nano-Structured Surface for Enhanced High Heat Flux Thermal Management Via 3D Printing
The generation and management of heat accounts for nearly 90% of global energy consumption. This is particularly true in advanced fields such as Artificial Intelligence (AI), electric vehicles, data centers, and aerospace systems, where the generation of substantial waste heat leads to undesirable temperature rises in devices. To prevent device failure from overheating under high heat flux conditions, advanced thermal management techniques with high heat transfer coefficients (HTC) and critical heat flux (CHF) capabilities are essential.
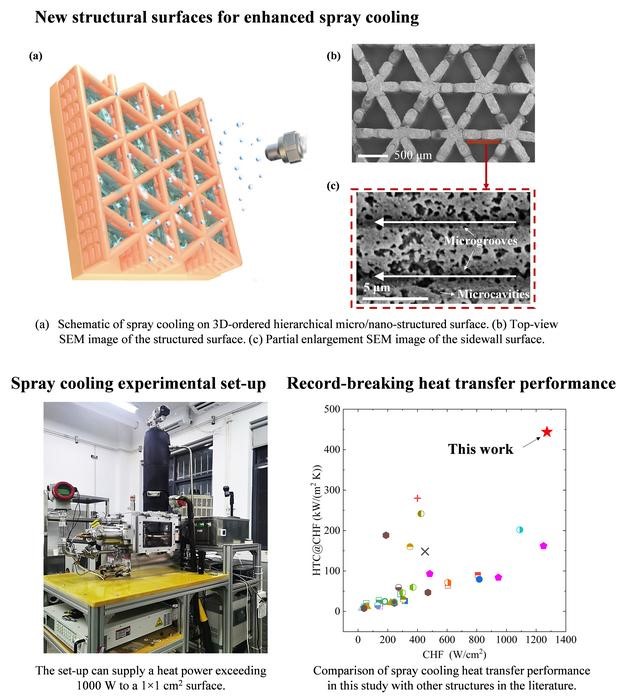
Figure 1. D Printed Hierarchical Micro/Nano-Structured Surface for Improved High Heat Flux Thermal Management
Among various cooling technologies, spray cooling is a promising active method that operates with a low degree of superheating, making it ideal for managing thermal challenges in high heat flux systems. This process involves atomizing a liquid into micro-droplets that are sprayed onto a surface, forming a liquid film. Spray cooling relies on three primary heat transfer mechanisms: forced convection, liquid film evaporation, and nucleate boiling. Figure 1 shows D Printed Hierarchical Micro/Nano-Structured Surface for Improved High Heat Flux Thermal Management.
To further improve the heat transfer efficiency of spray cooling, numerous approaches have been explored. For instance, increasing the spray flow rate enhances single-phase convection and raises the CHF, but this often results in a reduction in HTC. Utilizing micro/nano-structured surfaces has been shown to boost boiling heat transfer and increase HTC. However, intense boiling on these surfaces can cause vapor bubbles to accumulate and form a vapor blanket, which hinders significant improvements in CHF for spray cooling.
To overcome this issue, Professor Ronggui Yang from Peking University, in collaboration with a research team from Huazhong University of Science and Technology, combined high-precision 3D printing of resin with template-assisted electrodeposition to create a 3D-ordered hierarchical micro/nano-structured surface. This innovative surface optimizes the movement of spray droplets, capillary liquid films, and boiling bubbles, enhancing liquid film boiling and capillary evaporation, leading to improved heat flux and HTC. This approach achieved a record-breaking spray cooling heat transfer performance, with a maximum heat flux of 1273 W/cm² and an HTC of 443.7 kW/(m²·K).
The newly developed structured surface is expected to play a crucial role in the thermal management of high heat flux electronics such as high-power chips, laser weapons, aircraft rectifiers, and automotive power electronics. This method can be further adapted for practical applications involving multiple heat sources or large-scale cooling needs through the use of multiple nozzle arrays.
Source: EureAlert
Cite this article:
Priyadharshini S (2024), “Hierarchical Micro/Nano-Structured Surface for Enhanced High Heat Flux Thermal Management Via 3D Printing”,AnaTechMaz, pp. 288