The Development of Metal 3D Printing Technology
Metal 3D printing is considered the apex of all 3D printing. When it comes to strength and durability, there’s nothing quite like metal. [1] The first patent for metal 3D printing was DMLS (direct metal laser sintering) and it was filed in the 1990s by the German company EOS. Ever since then, engineers have come up with other methods for printing with metal, some of which are entirely unique and some that are just different enough from DMLS to be awarded their own patents. The Metal 3D printing is shown in figure 1.
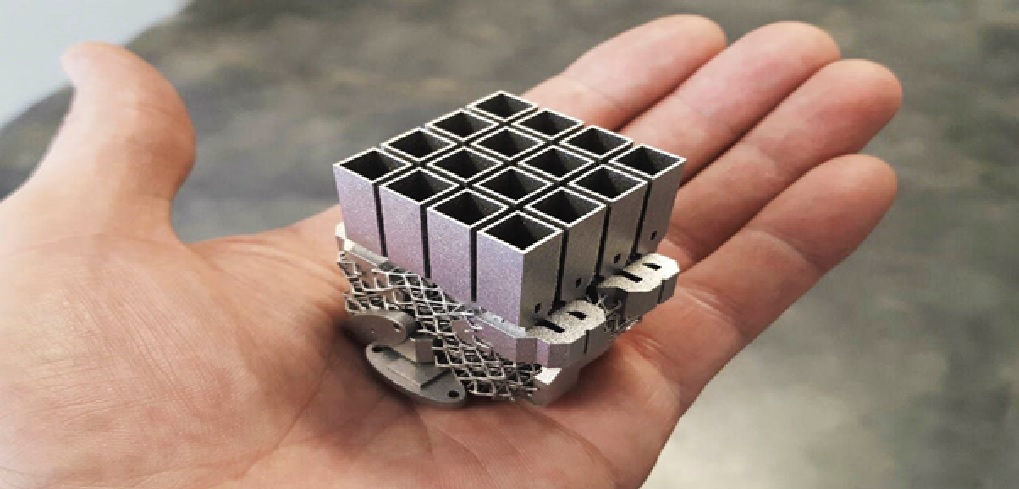
Figure 1: The Metal 3D Printing
Metal 3D printing provides a proven menu of benefits to a growing number of industries. Not only can you create parts with shapes and internal structures that could not be cast or otherwise machined, but metal 3D printing can create parts within parts so engineers can design a complex assembly in one piece. [2] This saves the time and labor of assembling parts or performing processes, such as welding, and increases efficiency of the final part.
Metal additive manufacturing makes it possible to quickly create functional prototypes made out of the same material as production components. The technology also makes creating specialized metal components for high-tech areas, such as aerospace far less expensive and time consuming. To top it off, there’s also far less waste in metal 3D printing, reducing the cost of printing in titanium, precious metals, and specialized alloys.
Metal 3D Printing holds a unique position in modern-day product development. [3] It allows for the direct manufacturing of complex end-use parts and facilitates tooling for conventional manufacturing technologies, reducing costs and lead times. This technology is also known as Direct Metal Laser Sintering (DMLS) and Selective Laser Melting (SLM).
Support structures are always required in metal printing, [4] due to the very high processing temperature and they are usually built using a lattice pattern.
Support in metal 3D printing serves 3 different functions:
- They offer a suitable platform for the next layer to be built upon.
- They anchor the part to the build plate and they prevent warping.
- They act as a heat sink drawing heat away from the part and allowing it to cool at a more controlled rate.
In traditional manufacturing, making metal parts is a wasteful process. When aircraft manufacturers make metal parts, as much as 90% of the material is cut away. [5] Using the 3D process, less energy is used and waste is reduced to a minimum. Finished 3D printed products can be up to 60% lighter than their machined counterparts.
Before we dive into the metal 3D printing technologies, [6] it is important to understand the following terms.
- Sintering: Sintering means heating the material (or particles) to the point of liquefaction but not completely melting them. The sintering temperature is always less than the melting temperature.
- Green State: A state of the metal 3D printed part where the metal particles are held together by the use of binder/binders material.
- Debinding: This is the process of removing the binder material from the green part.
- Furnace Sintering: This step follows the debinding process. In the furnace, the metal 3D printed part is sintered which fuses the metal parts to form highly dense solid parts.
References:
- https://3dprinting.com/metal/types-of-metal-3d-printing/
- https://all3dp.com/1/3d-metal-3d-printer-metal-3d-printing/
- https://www.materialise.com/en/manufacturing/3d-printing-technology/metal-3d-printing
- https://www.hubs.com/knowledge-base/introduction-metal-3d-printing/
- https://www.manufacturingtomorrow.com/article/2019/06/the-technology-of-3d-metal-printing/13492
- https://manufactur3dmag.com/a-comprehensive-list-of-metal-3d-printing-technologies/
Cite this article:
Vinotha D (2021) The Development of Metal 3D Printing Technology, AnaTechmaz, pp 1