Making Every Effort in The Mab Manufacturing Process
The biopharma industry is making significant strides in antibody development, but it also faces challenges in bulk monoclonal antibody (mAb) manufacturing. Ensuring compliance with good manufacturing practices (GMP) for mAbs is becoming increasingly crucial in this context. To shed light on the bottlenecks and potential solutions in bulk mAb manufacturing, BioPharm International® interviewed Lee Seung-sun, the lead scientist for the Manufacturing Science and Technology team at Samsung Biologics.[1]
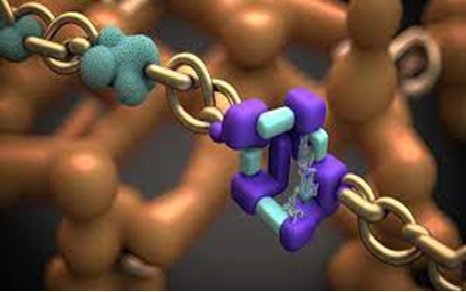
Figure .1 Making Every Effort in The Mab Manufacturing Process
difficulties with purification
Figure 1 shows Lee Seung-sun from Samsung Biologics highlights that the rise of intensified and continuous processes in biopharmaceutical manufacturing has led to higher cell numbers and titers in many products. As a result, perfusion techniques have been introduced at the N-1 or N stage of the cell culture process, and process development has involved using more concentrated feeds. However, with the increase in titers, the purification process has become the bottleneck, necessitating a transition to continuous processing and automation platforms.
The traditional workflow process of cell culture to purification to fill/finish is unable to effectively respond to the rapidly changing market demands for various modalities, including antibody drug conjugates (ADCs). To meet these challenges, continuous investment and rapid adoption of new technologies are required in the manufacturing process.
The COVID-19 pandemic has further exacerbated the situation by disrupting the global supply chain. It has become challenging to procure raw materials in sufficient quantities and at the right time. This issue is particularly significant for the manufacturing of mAb drug substances, where finding alternative raw materials is a complex task. Even if alternative materials are identified, it will take substantial time and effort to assess the associated risks and integrate them into the manufacturing process effectively.
In summary, the increase in cell numbers and titers has shifted the bottleneck from cell culture to the purification process. This necessitates the adoption of continuous processing and automation platforms. Additionally, the demand for various modalities and the disruptions caused by the COVID-19 pandemic highlight the need for continuous investment and the rapid incorporation of new technologies in the biopharmaceutical manufacturing industry.
Process analytical technology (PAT) deployment has improved the mAb manufacturing process as a whole.
The use of in-line sensors, such as Raman, in biopharmaceutical manufacturing has enabled more immediate responses to issues and improved process fine-tuning compared to the past. The acquisition of more data through these sensors has contributed to the accumulation of process knowledge. However, to fully leverage the benefits of Process Analytical Technology (PAT), a system that allows for the real-time use of information sensed by these in-line sensors needs to be established. This implies the need for an automated manufacturing facility that operates based on electronic batch records. Such a system would require a significant investment.
The implementation of PAT is driving the transition from traditional process control to predictive process control in the biopharmaceutical industry. This shift emphasizes the importance of data science in optimizing manufacturing processes. By establishing continuous processes in automated facilities using PAT, it becomes possible to manufacture high-quality monoclonal antibody (mAb) drug substances in less time and at a lower cost compared to traditional manufacturing methods.Samsung Biologics recognizes the need for digital transformation to keep up with these changes. They are actively working towards implementing advanced digital technologies and automation to enhance their manufacturing capabilities and stay at the forefront of the industry.
In conclusion, the biopharmaceutical industry is working tirelessly to improve the manufacturing process of monoclonal antibodies (mAbs). Companies like Samsung Biologics are investing in intensified and continuous processing, automation, and the use of in-line sensors like Raman. The goal is to enhance efficiency, product quality, and cost-effectiveness. The implementation of Process Analytical Technology (PAT) enables real-time decision-making and predictive process control. This requires a focus on data science and digital transformation, with an emphasis on advanced analytics and automation. Overall, the industry is committed to continuous improvement and leveraging new technologies to meet the evolving demands of the market and deliver high-quality mAb therapies to patients efficiently.
References:
- https://www.biopharminternational.com/view/pulling-out-all-the-stops-in-mab-manufacturing
Cite this article:
Janani R (2023),Making Every Effort in The Mab Manufacturing Process, AnaTechMaz, pp.187