The Role of Smart Sensors in Enhancing Precision and Efficiency in Industrial Robotics
The industrial robotics sector is seeing substantial growth, with around four million robots in operation, as reported by the International Federation of Robotics. Advances in robotic grippers have played a key role in driving this growth, but is there still potential for further advancements? Ross Turnbull, Director of Business Development and Product Engineering at ASIC design and supply company Swindon Silicon Systems, delves into the possibilities.
The Importance of Robotic Grippers
Industrial robots are increasingly tasked with a variety of jobs, from moving heavy goods to assembling delicate items, and grippers are essential for enabling them to handle objects effectively [1]. However, it’s not just about opening or closing the gripper. These robots must work with a diverse range of objects, varying in shape, size, and material hardness, and adapt accordingly.
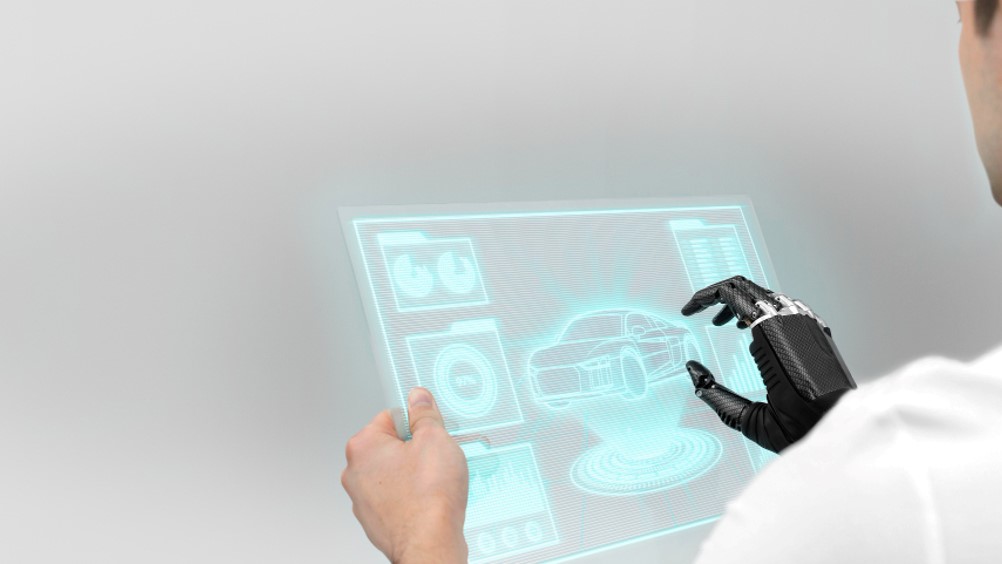
Figure 1. The Impact of Smart Sensors on Advancing Precision and Efficiency in Industrial Robotics
This presents a challenge. The gripper must quickly and accurately sense the object to secure it, but it can't apply excessive force, which could damage the gripper or the item. For example, delicate electronic components, such as thin connector wires, can easily be bent or broken if handled improperly. Gripper manufacturers strive to avoid these issues. Figure 1 shows The Impact of Smart Sensors on Advancing Precision and Efficiency in Industrial Robotics.
To ensure proper handling and minimize damage, robotic grippers must be equipped with at least one sensor. These sensors need to be highly accurate and precise to allow the gripper to handle objects efficiently and safely. So, how can we develop sensors that meet these requirements?
Guaranteeing Correct Positioning
To ensure the gripper moves with precision, it must have an accurate understanding of its position. This is where position sensors are essential.
Two common types of position sensors are inductive and optical. Inductive position sensors detect metallic objects using electromagnetic induction, where conductive targets disturb the magnetic field, which the sensor then detects. On the other hand, optical position sensors utilize an LED and photodetector, along with an optical scale, to measure linear displacement with exceptional accuracy.
Force Measurement in Robotics
Force and torque sensors are essential for providing robots with the ability to sense and respond to pressure. While humans can instinctively feel force, robots lack this natural sensation. By incorporating torque sensors, robots can gain a sense of 'feeling'. These sensors generally use strain gauges to convert pressure into an electrical signal, and when multiple gauges are combined, they can measure both the intensity and direction of force. This technology allows robots to handle delicate materials or perform tasks like precisely tightening screws without overapplying force and damaging the product.
Measuring Proximity
Another crucial sensor type is the proximity sensor, which plays a key role in verifying the angle of the jaw grippers for precise movement and even confirming the part while it remains in the gripper. Industrial robots frequently rely on proximity sensors for these functions.
Typically, inductive proximity sensors are used in this context. By leveraging electromagnetic principles and Eddy currents, these sensors can detect the metal of the gripper jaws or a metal target attached to them.
Improving Sensor Systems
Whether a system incorporates a single sensor type or a combination, one thing remains constant: the presence of at least one integrated circuit (IC). The sensor types discussed earlier typically generate an analog signal output. To be interpreted by the robot or industrial control system, this signal must be converted into a digital format.
Signal amplification, processing, and digitization can be handled by a standard off-the-shelf IC. However, for manufacturers seeking to differentiate their sensor technology, there is a more advanced solution available.
The Importance of Custom ICs in Robotic Grippers
This involves the use of an Application Specific Integrated Circuit (ASIC), a custom-designed chip tailored to meet the precise requirements of a particular application, such as a robotic gripper.
The advantage of this bespoke design is that the IC can be fully optimized for exceptional performance. ASIC designers collaborate closely with manufacturers to evaluate the existing sensor system and pinpoint areas where enhancements can be made for optimal results. For instance, sensor-specific processing functions can be incorporated to enhance signal quality, reduce noise, and ensure precise data accuracy, leading to more accurate robotic movements. In industrial robotics, where tasks involve handling delicate components like printed circuit board assemblies, the added precision from an ASIC is invaluable.
Additionally, an ASIC can significantly improve speed by minimizing latency, enabling real-time decision-making. This is especially crucial for robots operating in collaborative environments with humans, where quick responses are necessary to prevent collisions or other hazards in unpredictable settings.
The Future of Industrial Robotics Powered by Custom ICs
As products become increasingly complex yet smaller in size, manufacturing processes are becoming more challenging. However, upgrading plant machinery can provide a solution [2]. Custom ICs can address manufacturers' concerns about precision and reliability in industrial robotics, offering the dexterity and capabilities needed for modern manufacturing.
References:
- https://hokuyo-usa.com/resources/blog/role-sensors-robotic-automation-enabling-intelligent-and-adaptive-robotics
- https://www.eurekamagazine.co.uk/content/technology/the-role-of-smart-sensors-in-advancing-industrial-robotics-for-precision-and-efficiency
Cite this article:
Janani R (2025), The Role of Smart Sensors in Enhancing Precision and Efficiency in Industrial Robotics, AnaTechMaz, pp. 123