Pipeline Inspections with Mobile Robot Technology
In a groundbreaking study, the University of Bristol, under the leadership of Professor Bruce Drinkwater and Professor Anthony Croxford, has successfully demonstrated a novel inspection method for large pipe structures using mobile robots equipped with guided acoustic wave sensors. This innovative approach offers a cost-effective solution for inspecting pipelines with diverse defects, marking a significant advancement in the field.
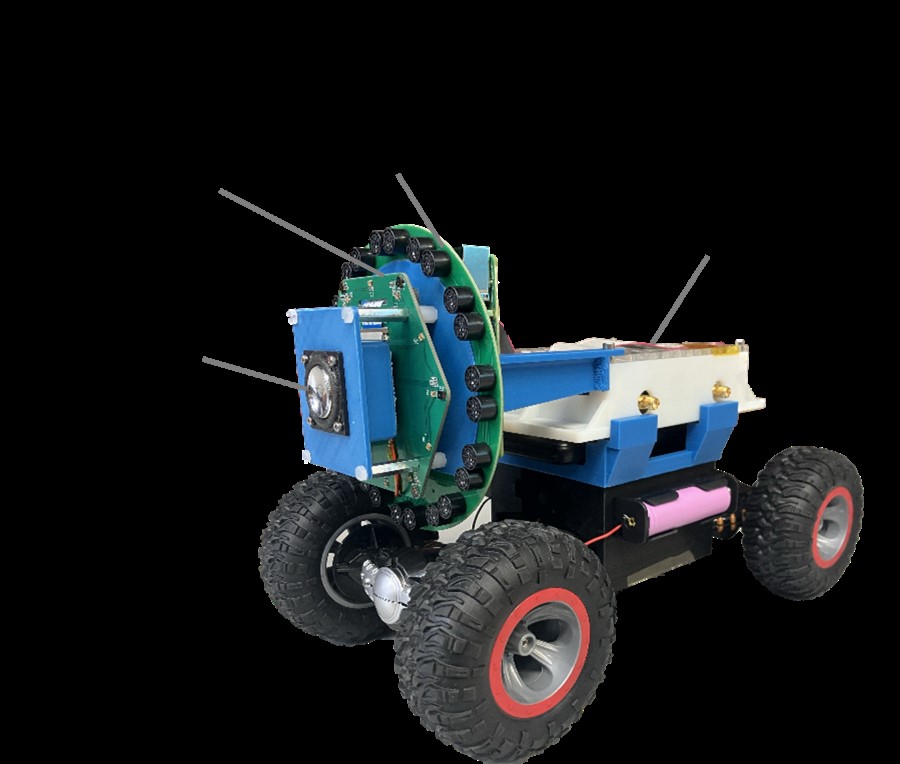
Figure 1. Pipebot. (Credit: Dr Jie Zhang)
The Methodology
Figure 1 shows the pipebot. Published in NDT and E International, the study showcases the team's ability to inspect a three-meter long steel pipe with various defects, including circular holes, crack-like defects, and pits. The inspection path was meticulously designed to achieve 100% detection coverage for a defined reference defect. The researchers utilized a network of independent robots, each carrying sensors capable of sending and receiving guided acoustic waves in pulse-echo mode.
Key Advantages
The approach presented by the University of Bristol team comes with several key advantages. By employing a network of independent robots, communication between them is minimized, eliminating the need for synchronization. This not only streamlines the inspection process but also opens up possibilities for on-board processing, reducing data transfer costs and overall inspection expenses.
Two-Stage Inspection Process
The inspection was divided into two crucial stages: defect detection and defect localization. This strategic division allows for a thorough examination of the pipeline, ensuring that no defects go unnoticed. Lead author Dr. Jie Zhang emphasized the importance of this approach in overcoming the limitations of existing robotic systems used for pipeline inspection.
Overcoming Challenges
While robotic systems with integrated ultrasound sensors have been utilized for pipeline inspection, they often struggle with varying pipe cross-sections and network complexity, leading to pipeline disruptions during inspection. The University of Bristol's innovative approach overcomes these challenges by deploying multiple robots for large area inspections.
Applicability and Future Prospects
The methods developed by the University of Bristol team are not only specific to steel pipes but are generally applicable to various scenarios involving different materials, pipe geometries, noise levels, and guided wave modes. This flexibility allows for the exploration of a wide range of sensor performance parameters, defect sizes, and operating modalities.
Collaboration for Real-World Implementation
With successful prototype demonstrations, the team is now poised to explore collaboration opportunities with industries to advance their prototypes for actual pipe inspections. The research is funded by the UK's Engineering and Physical Sciences Research Council (EPSRC) as part of the Pipebots project, showcasing the practical implications and potential industry applications of this groundbreaking technology.
The University of Bristol's innovative inspection method represents a significant leap forward in the realm of pipeline inspections. By harnessing the capabilities of mobile robots with guided acoustic wave sensors, the research opens up new possibilities for cost-effective, efficient, and non-disruptive inspections, ultimately contributing to the integrity and safety of critical infrastructure.
Source: University of Bristol
Cite this article:
Hana M (2023), Pipeline Inspections with Mobile Robot Technology, AnaTechmaz, pp. 9