Scientists Develop New 3D Printing Technique to Replicate Nature’s Strongest Fibers
Scientists are investigating innovative ways to replicate nature’s diverse and valuable features. Fine hairs and fibers, found throughout the natural world, serve a range of functions—from sensory perception to enhancing the unique texture of hagfish slime.
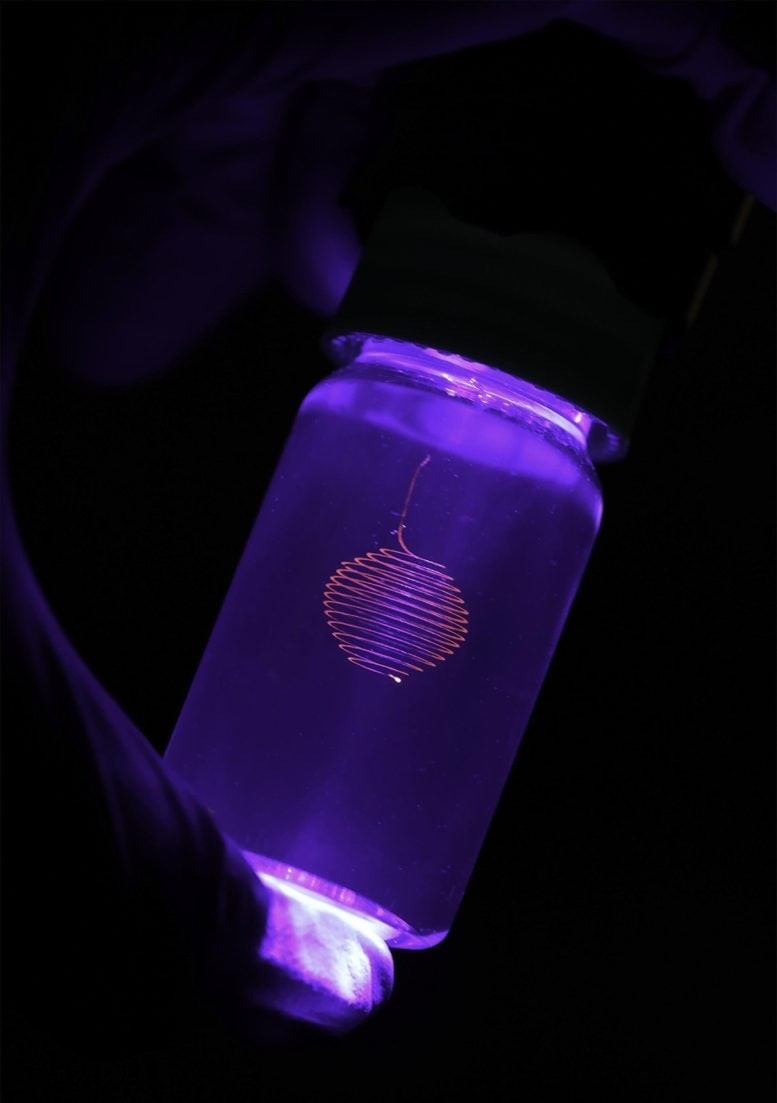
Figure 1. New 3D Printing Method Replicates Nature’s Toughest Fibers.
MechSE Professors Sameh Tawfick and Randy Ewoldt, along with doctoral candidate M. Tanver Hossain and external collaborators, have tackled this challenge with an advanced embedded 3D-printing technique. Recently published in Nature Communications, their research details a bioinspired method for rapidly printing fine fibers within a gel medium. Figure 1 shows New 3D Printing Method Replicates Nature’s Toughest Fibers.
Unlike traditional 3D printing, which deposits material layer by layer in open air, embedded 3D printing uses a support medium like hydrogel. In conventional methods, complex structures require additional, often disposable, support layers to maintain stability. Printing within a gel eliminates this need, as the gel itself provides structural support, enabling the efficient creation of intricate shapes like helical springs. Additionally, the printed object can be cured within the gel and later removed, allowing the gel to be reused for multiple prints, making the process more efficient and sustainable.
However, embedded 3D printing has historically faced challenges in producing extremely thin features, similar to the limitations of printing in air. Filaments thinner than sixteen microns would often break before curing due to surface tension. To overcome this, the research team aimed to print even finer diameters, replicating natural fibers like spider silk and the defensive threads secreted by hagfish.
Overcoming Limitations with Solvent Exchange
“In nature, there are many examples of filamentous structures that achieve a diameter of only a few microns,” said Hossain, the study’s second author, who focused on designing the non-Newtonian gel. “We knew it had to be possible.”
To prevent filament breakage caused by surface tension, the researchers utilized a solvent exchange method. “We modified the gel and the print ink so that the ink would cure as soon as it was deposited in the gel,” Hossain explained. “This prevents the filament from snapping because it’s almost instantaneously solid.”
Using this technique, the team achieved an impressive resolution of 1.5 microns. They also explored multi-nozzle printing, further accelerating the manufacturing process.
Advancing 3D Printing for Bioinspired Materials
“This research overcomes a long-standing limitation of 3D printing technology—printing soft materials with a diameter as small as one micron,” said Eom, who led the development of the solvent exchange process. “Achieving such high printing resolution means we now have the technological foundation to mimic the microfibers and hair-like structures found in nature, which exhibit remarkable functionalities.”
The team became interested in embedded 3D printing due to its potential to replicate the unique properties of hagfish slime, which owes its exceptional mechanical performance to micron-scale thread bundles. Ewoldt has been studying the mechanics of hagfish slime for over a decade, collaborating with Professor Douglas Fudge from Chapman University.
Implications for Advanced Materials and Engineering
“We adopted embedded 3D printing as a method to mimic these threads,” Eom explained. “Through our research, we discovered that developing high-resolution embedded 3D printing technology enables us to replicate a much wider range of natural structures than we initially expected.”
Expanding Possibilities for Fine Microstructures
“The significance of this method is that it allows us to produce a wide range of hair-like geometries without the challenge of gravity affecting such fine and flexible structures,” said Tawfick, who has been showcasing the technique’s potential applications. “This enables the creation of complex 3D hair structures with fine diameters using an ultraprecise 3D printer.”
“This method holds significant potential, as ultra-fine and long fibers could be combined with functional materials to replicate nature-inspired fibrous structures,” Hossain noted.
Eom added, “We are particularly interested in printing fine microstructures that cannot be achieved with today’s conventional semiconductor manufacturing techniques.”
Source: SciTECHDaily
Cite this article:
Priyadharshini S (2025), Scientists Develop New 3D Printing Technique to Replicate Nature’s Strongest Fibers, AnaTechMaz, pp. 140