Advancement in Implant Technology: Development of 3D-Printed Metals with Infection Resistance
In a groundbreaking development, researchers at Washington State University (WSU) have unveiled a novel surgical implant with the potential to revolutionize infection control in common surgeries, such as hip and knee replacements. The implant, detailed in the International Journal of Extreme Manufacturing, exhibited an impressive 87% efficacy in eliminating bacteria responsible for staph infections in laboratory tests. This innovation addresses a critical issue in the field, as bacterial colonization is a leading cause of implant failure and post-surgery complications.
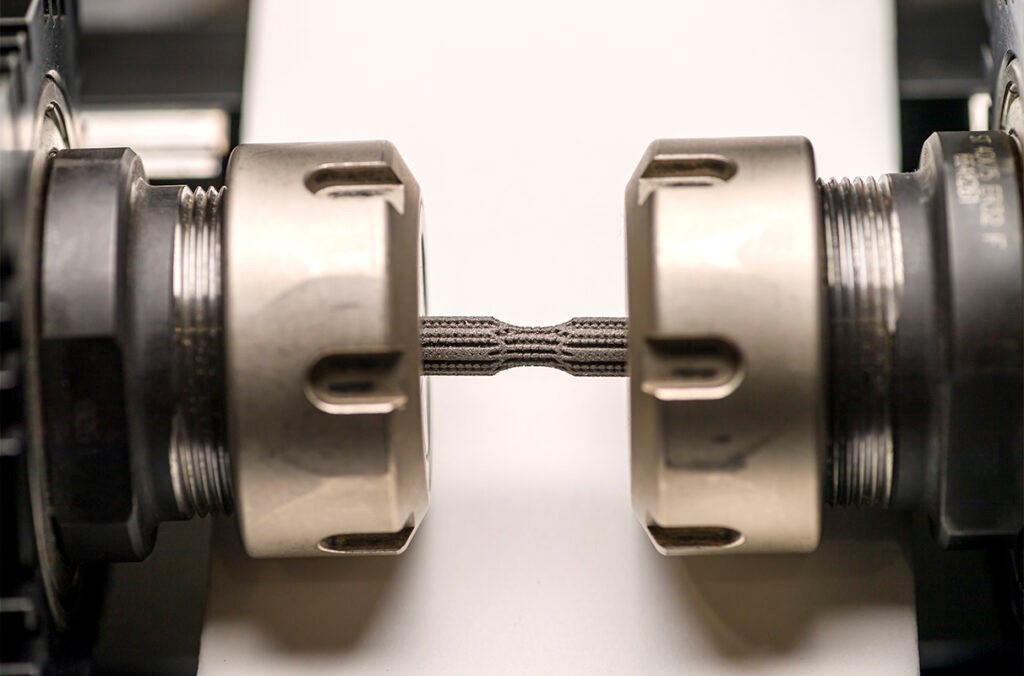
Figure 1. New 3D-Printed Material. (Credit: WSU Photo Services)
The Challenge of Infections
Figure 1 shows WSU researchers tested the new 3D-printed material's resistance to fatigue. Amit Bandyopadhyay, Boeing Distinguished Professor in WSU's School of Mechanical and Materials Engineering, highlighted the persistent challenge of infections in implant surgeries. Conventional implants lack inherent defenses against infections, relying primarily on antibiotic treatments. The need for a more proactive solution led the researchers to explore changing the material itself to impart antibacterial properties.
Materials Evolution
Titanium alloys, utilized in surgical implants for over 50 years, face limitations in overcoming infections. The WSU researchers utilized 3D-printing technology to enhance the titanium alloy with 10% tantalum, a corrosion-resistant metal, and 3% copper. This modification proved instrumental in disrupting bacterial cell walls upon contact with the material's copper surface. Simultaneously, tantalum promoted healthy cell growth, expediting the healing process.
Multifunctional Advantages
Co-author Susmita Bose, Westinghouse Distinguished Professor, emphasized the multifunctional advantages of the modified implant. By integrating infection control and promoting bone tissue integration, the researchers aim to address the dual challenges faced in implant surgeries today. The goal is to achieve a bacterial death rate exceeding 99% without compromising tissue integration.
Comprehensive Study and Future Prospects
The research spanned three years, encompassing a thorough assessment of the implant's mechanical properties, biological responses, and antibacterial capabilities in both laboratory settings and animal models. The team also scrutinized wear and toxicity aspects, ensuring the safety and effectiveness of the implant. Ongoing efforts involve further refinement to enhance bacterial death rates and validate performance under real-world conditions.
Path to Commercialization
Collaborating with WSU's Office of Commercialization, the researchers have filed a provisional patent for their groundbreaking implant. Funding from the National Institutes of Health supported this transformative project, which also involved collaboration with researchers from Stanford University and WSU's College of Veterinary Medicine.
This innovative surgical implant marks a significant stride toward addressing the pervasive issue of infections in implant surgeries. With the potential to enhance infection control and tissue integration, the WSU research paves the way for a new era in surgical interventions, offering hope for improved patient outcomes and reduced revision surgeries. The ongoing efforts and collaborations underscore the commitment to advancing this groundbreaking technology from the laboratory to real-world applications.
Source: Washington State University
Cite this article:
Hana M (2023), Advancement in Implant Technology: Development of 3D-Printed Metals with Infection Resistance, AnaTechMaz, pp. 57