After Two Decades of Research, Direct drive Plasma Etching Technology is Set to Revolutionize Chip Manufacturing
Imagine trying to carve an incredibly detailed miniature sculpture into a space no larger than your fingernail—over and over again, billions of times, with virtually zero tolerance for error. That’s essentially what semiconductor manufacturers do when etching intricate patterns onto silicon to produce the chips powering nearly every modern device.
As the demand for faster, smaller, and more powerful electronics grows—especially in fields like artificial intelligence—the need for ultra-precise etching has become increasingly critical. Addressing this challenge, researchers have unveiled a groundbreaking technology known as DirectDrive, which dramatically enhances the precision of plasma etching used in chip fabrication. This breakthrough could play a pivotal role in the production of next-generation electronics, enabling denser, faster circuits.
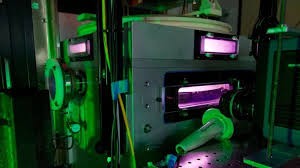
Figure 1. The plasma etching machine setup.
Two Decades in the Making
DirectDrive is the result of a 20-year research effort. The idea originated in 2006, when UCLA engineer Patrick Pribyl envisioned a better way to control the plasma used during the etching phase of chip manufacturing. He developed a concept for rapidly switching radio frequency (RF) energy to allow for far more precise control over plasma behavior.
To test his theory, Pribyl built a rough prototype of an RF switching system—right in his own kitchen. But despite its promise, the industry wasn’t ready to embrace the technology. The underlying science needed more development, and scaling a homemade device into industrial hardware would take years. Figure 1 shows the plasma etching machine setup.
Refusing to abandon the idea, Pribyl teamed up with UCLA physicist Walter Gekelman. With limited funding and resources, they pressed on, gradually attracting more collaborators over the next decade.
Unlocking Precision Through Pulsed RF Energy
The team conducted extensive experiments using lasers and custom-built setups, analyzing how plasma ions reacted to various RF energy pulses. They discovered that rapidly pulsing RF energy—turning it on and off thousands of times per second—offered unprecedented control over plasma behavior. This technique allowed for a much finer level of detail, akin to giving chipmakers a vastly more precise set of carving tools.
Traditional plasma etching systems struggled to switch power levels quickly, leading to inconsistencies. Pribyl’s DirectDrive method changed that—delivering power adjustments in just 50 microseconds, tens of thousands of times faster than existing systems.
Industry Adoption Begins
Now, the technology is finally seeing real-world use. Semiconductor manufacturers are integrating DirectDrive into their latest etching tools to produce the most advanced chips yet.
According to Lam Research, the company that now holds the patent for DirectDrive, the system is the first solid-state plasma source in the industry. It delivers 100 times faster responsiveness than previous technologies, significantly reducing defects in extreme ultraviolet (EUV) patterning processes.
DirectDrive represents not only a technological leap in chipmaking precision, but also a powerful reminder of the long-term innovation and persistence behind transformative breakthroughs.
Reference:
- https://interestingengineering.com/innovation/directdrive-plasma-etching-ultra-precise-chips
Cite this article:
Keerthana S (2025), After Two Decades of Research, Directdrive Plasma Etching Technology is Set to Revolutionize Chip Manufacturing, AnaTechMaz, pp.326