Direct Part Marking (DPM)
Direct Part Marking (DPM) is a technology used to produce two different surface conditions on an item. These markings can be created by laser etching, molding, peening, etc.
Traditional print quality measures are based on the assumption that there will be a measurable difference between dark and light elements of a symbol. Because DPM symbols frequently do not have sufficient contrast between elements intended to be dark and light, it is often necessary to provide specialized lighting in order to produce highlights or shadows in order to distinguish the various elements of the symbol.[1]
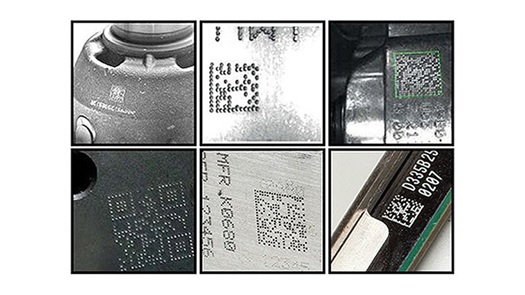
Figure 1. The direct part marking (DPM)
Figure 1 shows Codes, symbols, and text applied directly to a part’s surface (rather than affixed by a label or packaging) are known as Direct Part Marks (DPM). DPM are used widely in industrial part tracking from electronics manufacturing to automotive assembly. These marks are affixed directly to parts by abrading a part surface or marking in some other manner that cannot be discarded, torn, obscured, wiped off, or easily degraded. An example of an indirect mark is an inkjet code on a paper label or package, which can be removed from the part, damaged by physical contact, or distorted by moisture, temperature, and other elements.
An example of a direct mark is a code that is permanently etched directly onto the surface of a part, by a laser for example, which removes the surface layer of the substrate of a device to expose the code in a varying color or contrast. Other types of permanent marking include electrochemical etch and dot peen. These methods can also be used to abrade codes into identifier tags or plaques that can then be permanently affixed to a part.[2]
Many Marking Methods Are Available
There are many methods to directly mark objects. Selecting the best method for the application is critical to achieving success. Each method has its own advantages and limitations. Since each method has its own advantages and limitations, it is important to review and experiment with as many methods as possible before selecting the best one for your application.
Electrochemical Etch: This process uses a low voltage current to mark the object surface. This is commonly used for low volume product runs.
Ink Jet: This type of marking uses small , dots sprayed directly onto the surface. Ink jet produces high contrast marks. Ink jet is not considered a permanent marking method.
Laser Etch: Lasers etch the symbol directly onto a surface. Clean, high resolution marks are produced making laser-etch well-suited for automated environments.
Dot Peen: Dot peen is a percussive marking method, using changes in depth to create marks. Dot peen is recommended for applications where the symbol must last the entire life cycle. [3]
DPM Quality Guidelines Document
Acknowledging that current ISO print quality specifications for matrix symbologies and two-dimensional print quality are not exactly suited for DPM symbol evaluation, an ad-hoc committee under the supervision of the AIM Technical Symbology Committee developed a guideline to act as a bridge between the existing specifications and the DPM environment in order to provide a standardized image based measurement method for DPM that is predictive of scanner performance.
The document describes modifications which are to be considered in conjunction with the symbol quality methodology defined in ISO/IEC 15415 and two-dimensional symbology specifications. It defines alternative illumination conditions, modifications to the measurement and grading of certain parameters and the reporting the grading results.[1]
References:
- https://www.aim-na.org/aidc-technology.html
- https://www.microscan.com/en-us/resources/know-your-tech/direct-part-marking-dpm
- https://www.microscan.com/en-us/resources/know-your-tech/direct-part-marking-methods
Cite this article:
Thanusri swetha J (2021), Direct part marking (DPM), AnaTechMaz, pp. 24