Unleashing the Power of Solvent-Free Lithium-ion Battery Electrodes
Researchers at Worcester Polytechnic Institute (WPI), led by Yan Wang, have made a significant breakthrough in the production of lithium-ion battery electrodes. They have developed a solvent-free manufacturing process that offers several advantages over existing electrodes in terms of cost-effectiveness, environmental friendliness, and faster charging capabilities. This development holds great potential for enhancing the battery manufacturing industry, particularly in the production of batteries for electric vehicles. [1]
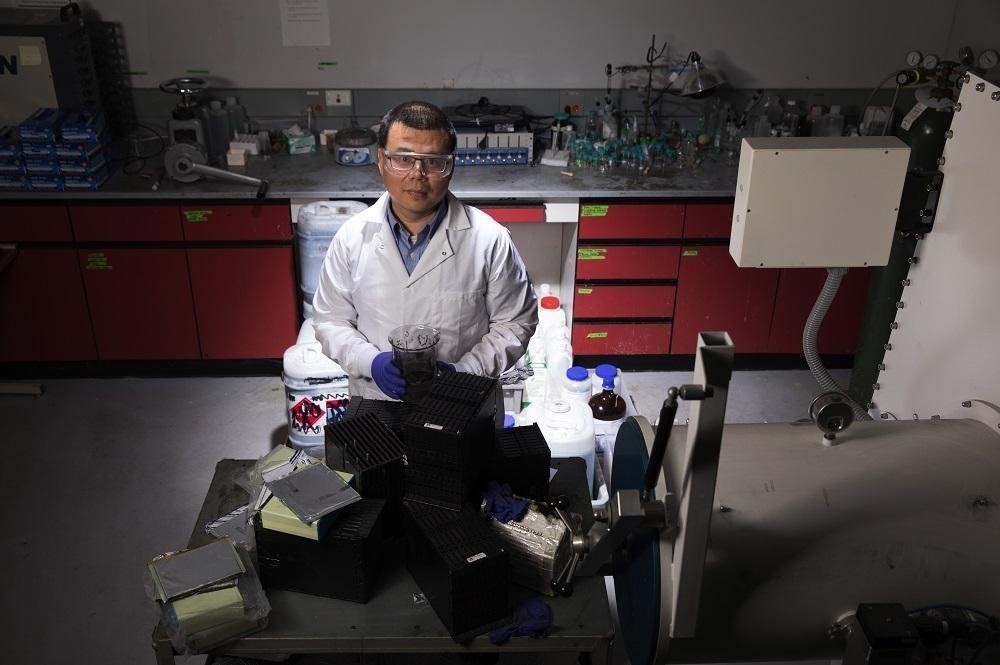
Figure 1. Yan Wang (Credit: Matt Burgos)
Figure 1 shows Worcester Polytechnic Institute researcher Yan Wang. In a recent publication in the journal Joule, the team unveiled their innovative dry-print manufacturing process, which eliminates the use of hazardous solvents and eliminates the lengthy drying periods typically associated with electrode production using traditional methods and slurries. Wang, the William B. Smith Dean's Professor in the Department of Mechanical and Materials Engineering at WPI, expressed that this novel approach has the potential to be easily scaled up, resulting in a remarkable reduction of up to 15 percent in electrode manufacturing costs. Moreover, the electrodes produced through this technique exhibit superior charging capabilities compared to those manufactured using conventional methods. [1]
“Current lithium-ion batteries charge too slowly, and manufacturers typically use flammable, toxic, and expensive solvents that increase the time and cost of production,” Wang said. “Our solvent-free manufacturing process addresses those disadvantages by producing electrodes that charge to 78 percent of capacity in 20 minutes, all without the need for solvents, slurries, and long production times.” [1]
In the conventional manufacturing process of commercial lithium-ion battery electrodes, a mixture of active materials, conductive additives, polymers, and organic solvents is combined to form a slurry. This slurry is then applied onto a metal substrate, dried using an oven, and subsequently cut into pieces for utilization in batteries. To recover the solvents used, a distillation process is employed. [1]
In contrast to the conventional method, the researchers' approach involved blending electrically charged dry powders, enabling them to adhere when sprayed onto a metal substrate. The resulting dry-coated electrodes were subsequently subjected to heating and compression using rollers. By bypassing the conventional drying and solvent recovery steps, the team achieved a remarkable 47 percent reduction in energy consumption during battery manufacturing, as reported by the researchers. [1]
Yan Wang has dedicated significant efforts to enhancing lithium-ion batteries and minimizing their environmental impact. He is also a co-founder of Ascend Elements, a company committed to developing battery recycling technologies. Wang's research on electrode manufacturing has received funding from the Department of Energy through collaborations with the United States Advanced Battery Consortium LLC and the Massachusetts Clean Energy Center. [1]
The project involved a collaborative effort, including the contributions of several individuals. This included Yangtao Liu, a Ph.D. candidate, Jinzhao Fu, a graduate student, Xiaotu Ma, an Assistant Research Professor, Panawan Vanaphuti, a Ph.D. candidate, and Rui Wang, a Ph.D. candidate, all from WPI. Additionally, researchers from Texas A&M University, Rice University, Microvast Inc., Argonne National Laboratory, and Brookhaven National Laboratory participated in the project, forming a diverse and multidisciplinary team. [1]
The manufacturing technology developed by Wang's team at WPI has shown such promise that the institute has filed a patent application to protect their innovative approach. Furthermore, Wang and his collaborator, Heng Pan from Texas A&M University, have taken their research a step further by co-founding AM Batteries Inc. This venture-backed company aims to collaborate with industry leaders such as Amperex Technology Limited (ATL) and other companies to accelerate the scaling up of solvent-free electrode manufacturing. This partnership highlights their commitment to bringing this technology to the commercial market and revolutionizing the battery industry. [1]
Source: WPI
References:
- https://www.wpi.edu/news/researchers-led-wpis-yan-wang-develop-solvent-free-process-make-better-cheaper-lithium-ion-battery
- https://scitechdaily.com/greener-cheaper-and-charging-faster-a-new-way-to-manufacture-lithium-ion-battery-electrodes/
Cite this article:
Hana M (2023), Unleashing the Power of Solvent-Free Lithium-ion Battery Electrodes, AnaTechmaz, pp.439